Building a semi acoustic guitar, hand carved from solid wood.
A whole lotta shaving going on!
In this blog post, we will take you through the process of how we craft a high quality custom arch top guitar, from the raw billet of wood to the nicely polished and shiny, finished instrument. More specifically, we’ll show you the building process of our T-Ultimate Cherry Burst, with some additional pictures of the T-Ultimate Dark Sunburst.
The building process can roughly be divided into four stages: Stage 1: Design, Stage 2: Woodwork, Stage 3: Painting, lacquering & polishing and fretting, Stage 4: Hardware & Electronics. The entire process can take up to six months, from the first moment we have a piece of wood in our hands, until the first time you will have your guitar in your hands.
How they are made
Almost all production processes are carried out by hand without the use of modern CNC-machines. However, we do have some machines like a band saw. For our builds, Dongming still uses the traditional construction methods that he mastered when he was an apprentice of a famous Chinese classical instruments builder in Beijing during the 90s. This is the same method that luthiers used 400 years ago when they first started building violins, and lends itself perfectly well for building semi acoustic (arch top) guitars like ours. Many of the used woodworking tools are made by Dongming himself. Here's where his former profession of electro-mechanic comes in handy.
Stage 1: Design
Lots of guitar talk
Building a Dejawu Guitar starts with making a design. At this stage, we thoroughly discuss all the details on how the end result should look. We decide (together with the customer) on the model, body size, wood type, combinations of wood, neck shape and length, body thickness, color, fret distance, nut width, bindings, inlays and so on. Options are endless.
To the drawing table
When all is decided, detailed drawings are made of the guitar with its exact measurements and specifications. With these drawings, plastic cut-outs are made which in turn function as a template for cutting out the different components of the guitar. After having completed these steps, it is now time to go on to the wood. The pictures below show a variety of different templates of guitar models that Dongming has built over the years.
Stage 2: Woodwork
Choosing the wood
All woods that we use for our guitars are chosen in the first place for their proven suitability and individual sound characteristics. These include (solid) flame maple, mahogany and spruce. Choosing the right type of wood is of utmost importance, if not the most important step in the process of building a guitar. We solely make use of solid tone woods. We very much prefer the tonal qualities of solid wood over laminated wood. In addition, the structure and shine of lacquered solid wood is much more evident. An inseparable consequence is that you never can order a guitar that looks exactly the same as one we have made before. We always have a sufficient number of tops and backs in stock.
Book matching
After we decided on the perfect piece of wood, the raw billet is then sawn in half (diagonally, in length). The sides of these two pieces are then book-matched and glued together. If possible, we not only book-match the two sides of a top or a back but also the top and back itself.
As you can see in the pictures, the figuring in the wood is clearly visible.
Carving the tops and backs
After rough wood cut-outs are made of these different parts, such as the body’s silhouette, we start shaving, carving, sculpting and sanding the wood. This is a very labor intensive and delicate process and requires a very steady hand. The wood we use for our guitars is not laminated and pressed into shape (as you can only carve solid wood :). Instead, the tops, backs and necks of our guitars are completely hand carved. A whole lotta shaving going on in his workshop, you could say!
The construction of our semi-acoustic guitars, all of which are equipped with a square center block at the bridge position, eliminates all possible feedback problems entirely while maintaining its acoustic properties. As you can see on the pictures below, the center of the top maintains its original thickness, while the rest of the wood is carefully carved away by hand. In this way, there is considerable less tension on the top compared to a top made out of laminated wood. Hand carving the top thus eliminates the need for a center block that covers the entire body length of the guitar for stability.
Making the f-holes
When the top has reached the right thickness, small holes are drilled to help cut out the f-holes. The rough shape is cut out with a hand saw and the fine shape is carved out by hand with a traditional woodcarving knife. The f-holes are then carefully trimmed with a binding and fixed with some tape to let the glue dry properly.
Molding the sides
After the top and back have been finished, we cut and bent the sides using a custom made wooden mold. This process requires some planning as the sides need to be attached to the tops and backs straight away in order to maintain its shape.
Attaching the sides
When the sides have adjusted to its new shape it can be glued to the back with the kerfing. Kerfing, also known as guitar lining, is tapered strips of wood with spaced slits that make it flexible. We glue this around the inside seems where the top and back are joined with the sides. We do this add strength and stability to the body when assembling it all together. The guitar is really starting to come together now! Hereafter we can proceed by gluing on the top.
Making the neck and fretboard
The neck also starts off as a raw billet of wood. Three of these pieces are enforced with a steel truss rod and then glued together. We then continue on by gluing on the head stock face and cutting it into shape. After this, the ebony fingerboard - which guarantees smooth playing - is glued on and the neck is carved into shape. The T-Ultimate has a C-profile neck shape. When this process is done, slots are made into the finger board. The neck is completed with a heel cap and a bone nut. Inlays on the neck are no standard feature on our guitars. Instead, little dots on the side of the neck help you orientate. However, inlays are always an option if you wish.
Applying the bindings to the body
After the whole body is assembled, we make a slot along the edges of the body using a hand router. After that, a seven-ply binding is glued to the sides and fixed with painters tape to keep it in place until the glue has dried.
Assembling the body
We can now proceed joining the body with the neck. It is really starting to come together now!
Stage 3: Painting, lacquering & Polishing
Dongming is a real artist in creating the most beautiful sunburst colors. Choosing the most beautiful combinations has become one of his specialties. As you can see in the pictures below, the figuring of the wood is popping out real nicely. All our guitars have a nitro-cellulose lacquer and are hand polished by Jin Youmei, receiving careful attention to highlight the individual character and ensuring a striking depth and clarity.
Preparing the fret board
After the guitar has received its color, the fret board is sanded to get its radius and is then completely cleaned up. This may not sounds like much, but is actually a very labor intensive job. After this, the slots for the frets are made.
Placing the frets
When the fret board is all smoothed, the fretting is done. One by one the frets are carefully placed in position, and then hammered into the fret board. The 25.5" scale of the T-Ultimate has 22 frets. The sides of the frets are then finished to eliminate all sharp edges completely. A very precise work!
Making the pick up holes
One of the last steps is drilling the pick up holes.
Final polish
When the pick up holes are in place, the guitar receives its final polish. Of course, I mean here: final polish for the moment, as polishing guitars is a never ending process.
Stage 4: Hardware & Electronics
When the woodwork, painting, lacquering and polishing is all done, the guitars are carefully packed and shipped to the Netherlands. High quality parts that can come up to the demands of professional players are hard to get and quite expensive in China. Therefore, all the assembly of the hardware and electronics, as well as adjustment and finishing touches are done by Derk Jan in his workshop at home in the Achterhoek in the Netherlands. Derk Jan also makes custom pick-up rings. As the arched top has its own specific features, no standard rings are available on the market so individual mounting rings are made of raw ebony. A special feature on most stock guitars is a six position Free-Way 3x3-05 toggle switch that allows both humbucker and single coil sounds. Of course, the wiring options can always be discussed.
T-ultimate CHERRY BURST in the spotlights
So, now we are four months and hundreds of man hours later, and the moment we have all been waiting for has finally arrived. Its done! Enjoy!
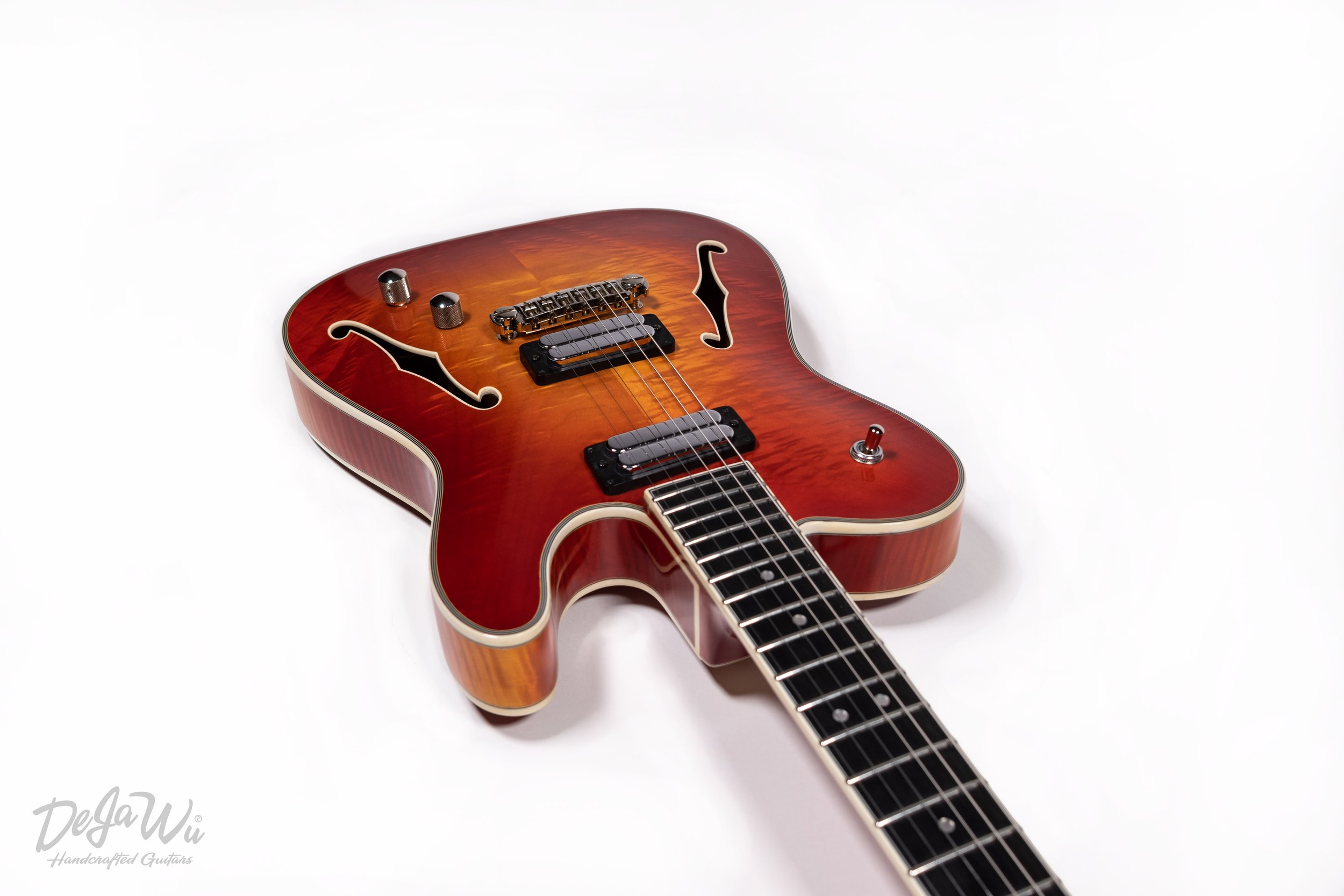
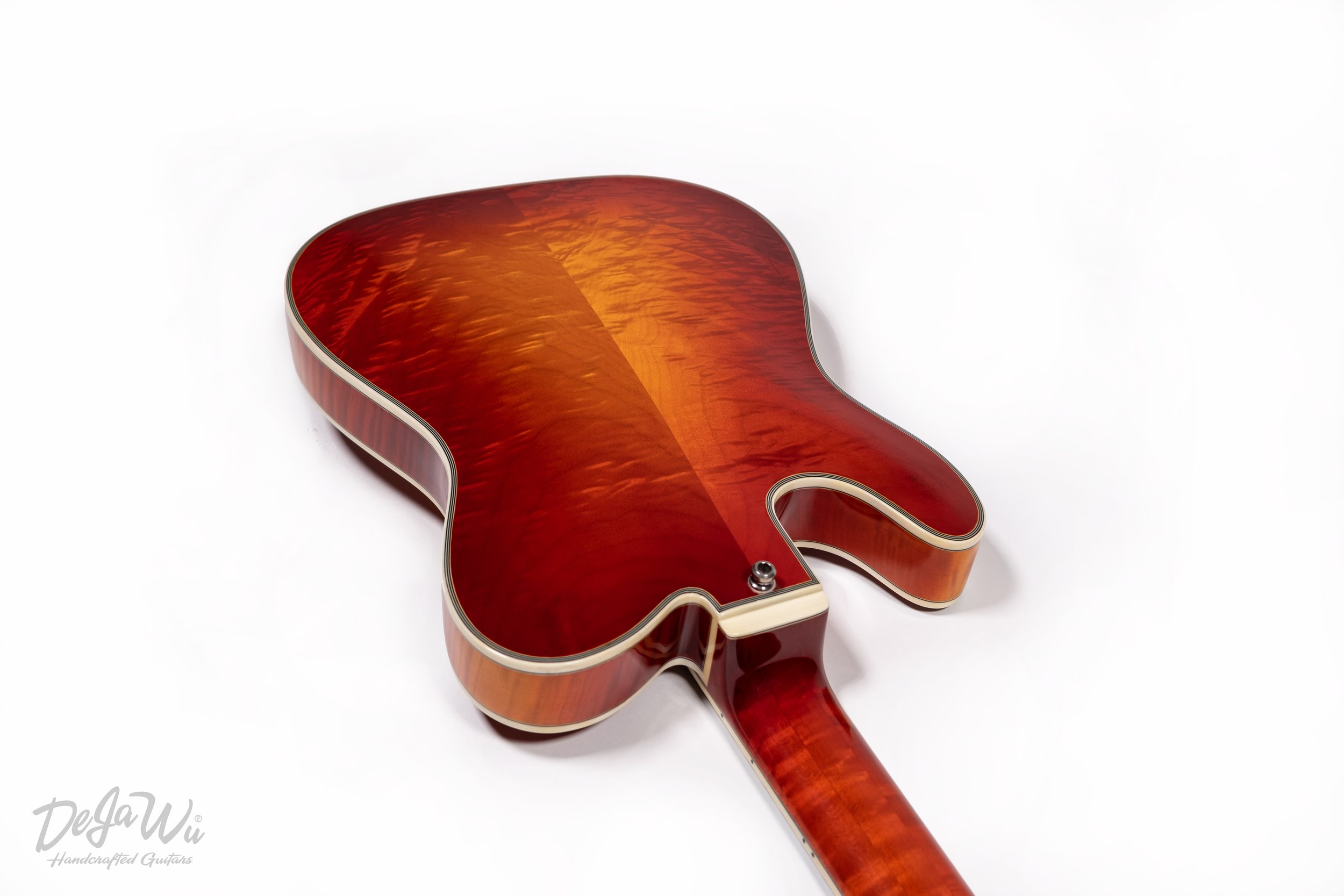
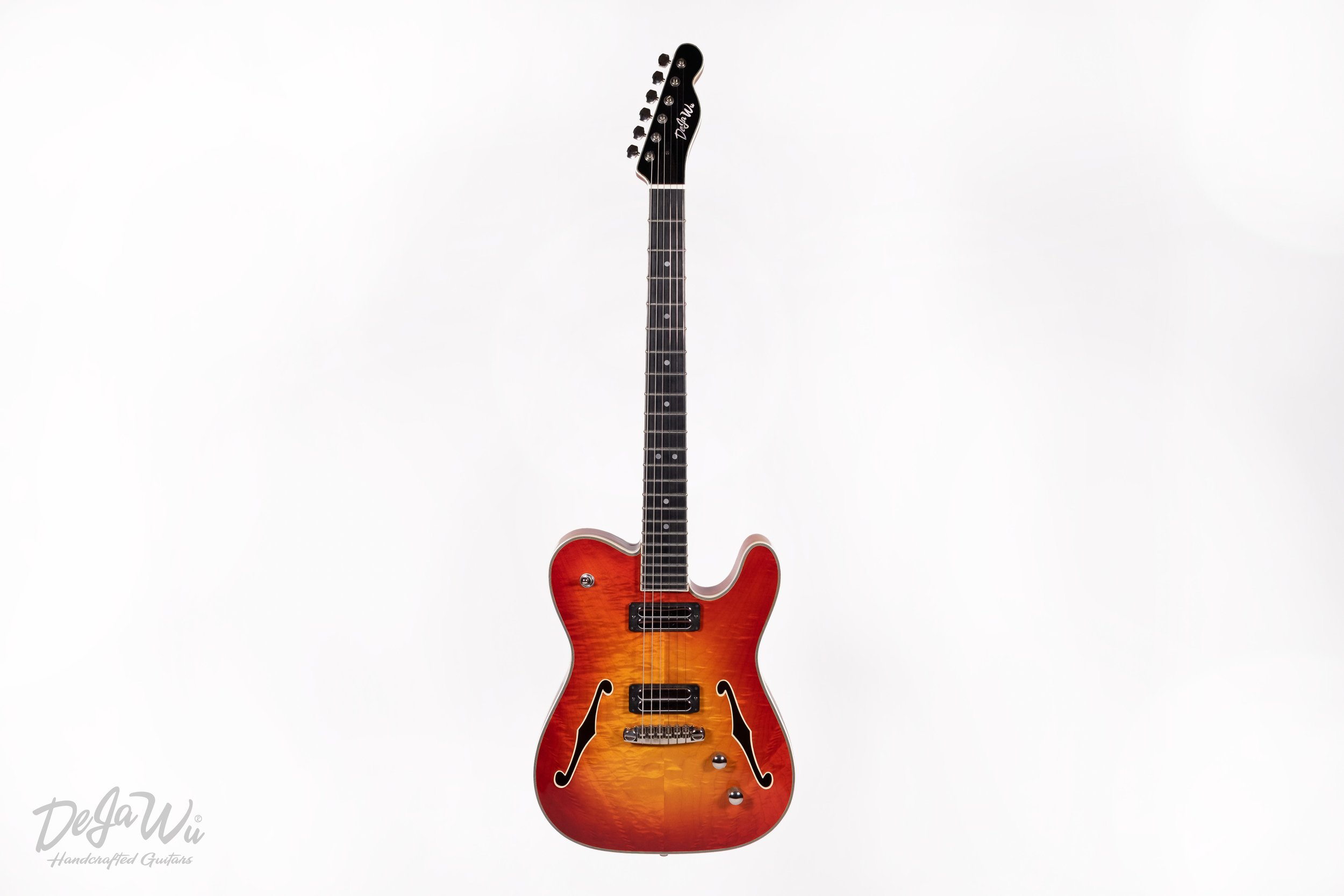
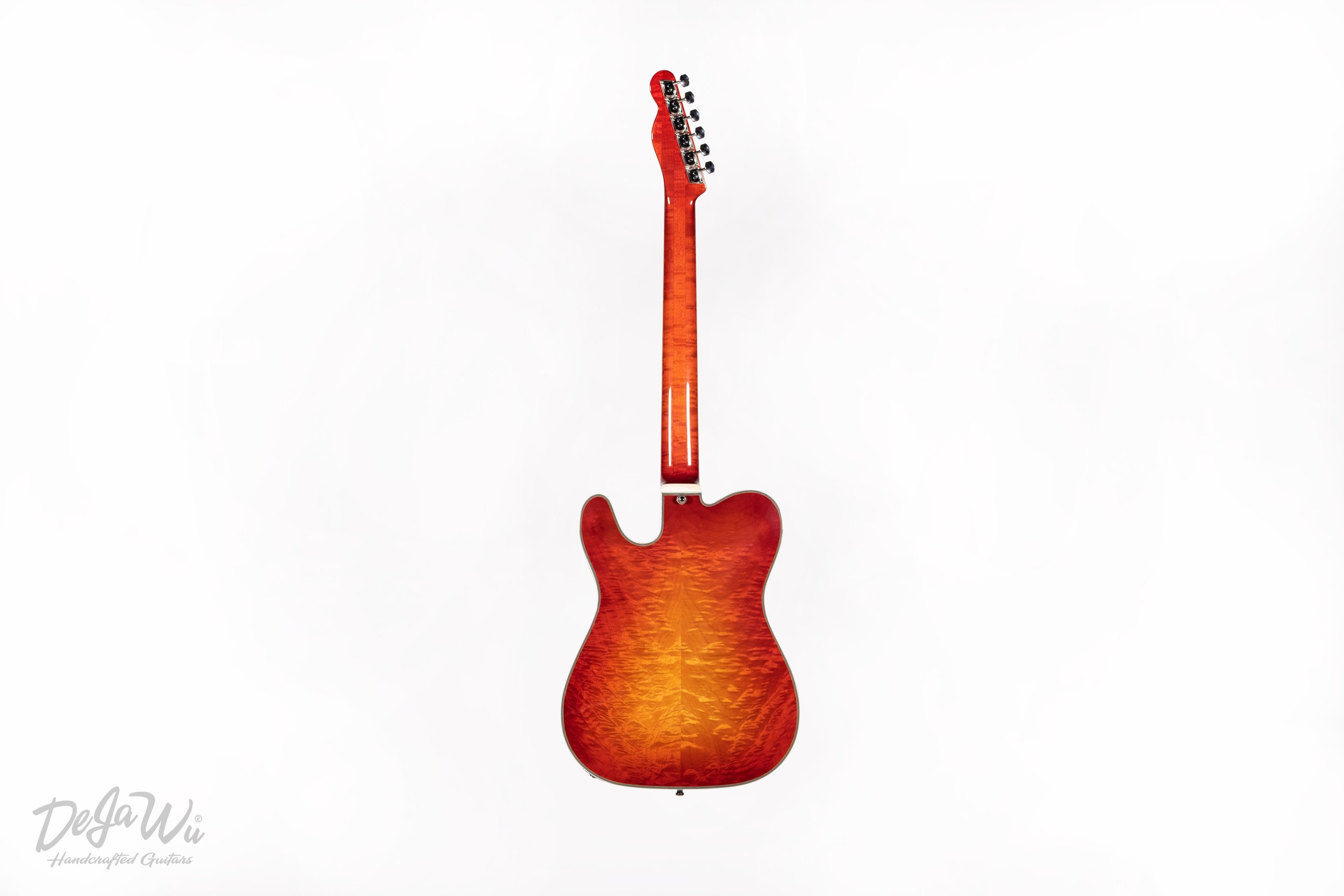

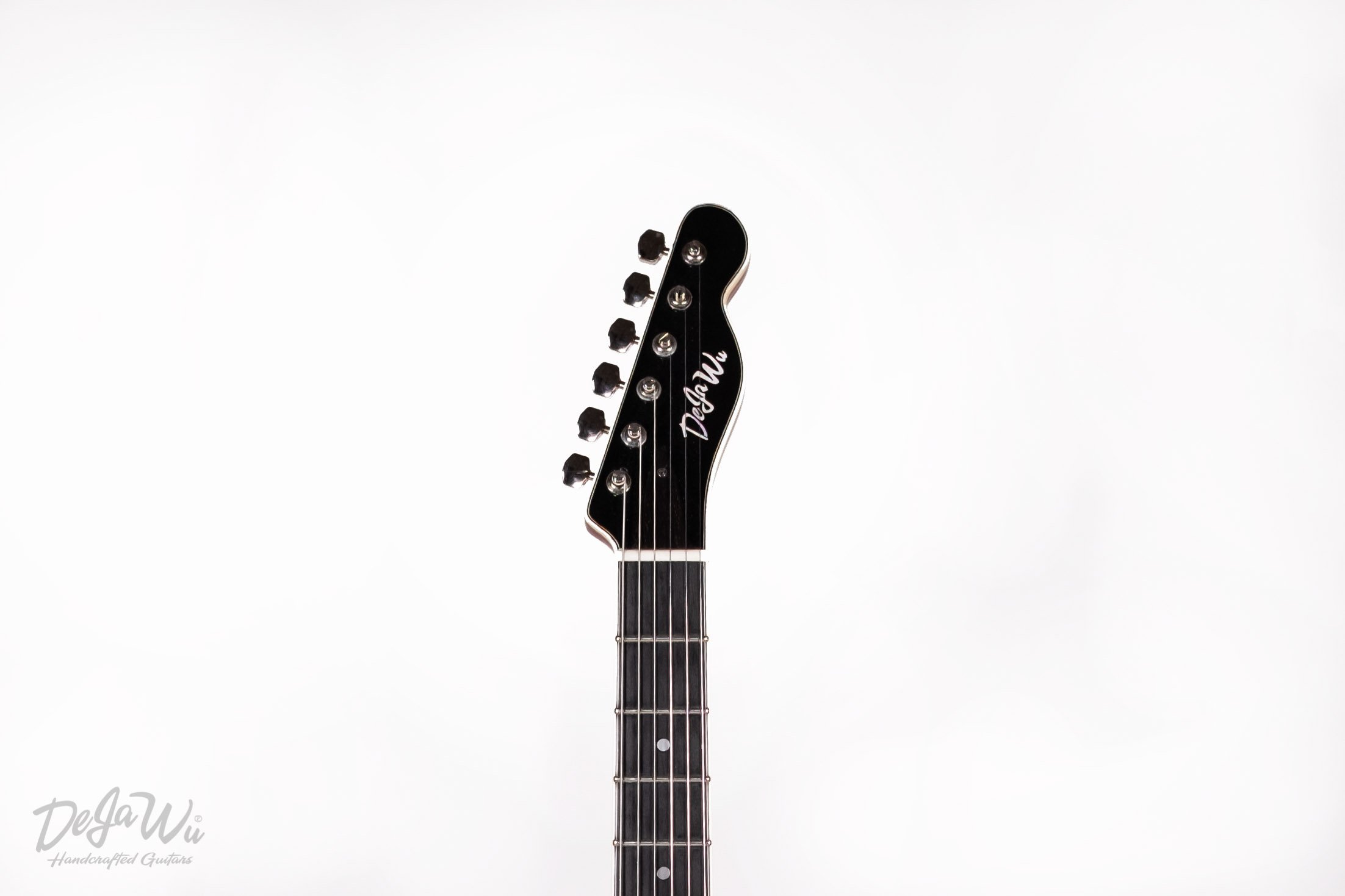
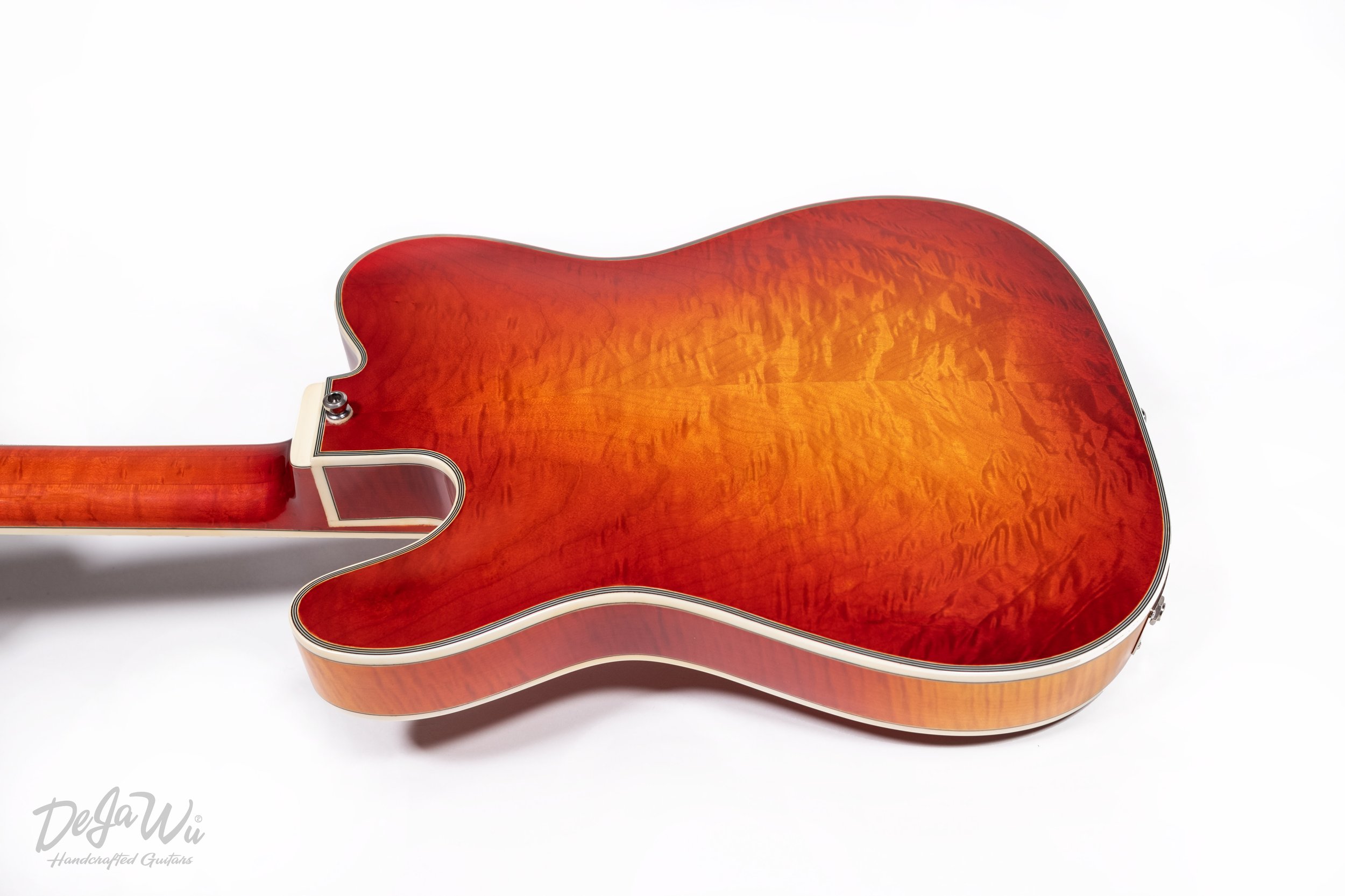
DESCRIPTION
The semi-hollow body of the Dejawu T-Ultimate Cherry Burst is completely hand carved from solid flame maple and trimmed with a seven-ply binding. The three-piece hand carved neck has an ebony fingerboard that guarantees very smooth playing. The 25.5" scale has 22 frets. This model has mother of pearl inlays and Häussel Double Tele pickups. String height is adjustable on the Schaller* Signum bridge and enables precise intonation as well as an excellent sustain. This specific model is equipped with a Free-Way 3x3-05 six-position toggle switch and a Push/Push tone pot. In position 1, 2 and 3 the pot switches between series and parallel. In the position 4, 5 and 6 it switches between inner and outer single coils.
Nut type: Bone
Nut width: 1.77''/ 45 mm
Width at Last Fret: 2.26'' / 57.4 mm
Scale: 25.5'' / 64.8 cm
Pickups: Häussel Double Tele
Switch: Free-Way Switch 3 x 3 – 05, Six positions
Controls: 1x Vol, 1x Tone push/push
Bridge/Tailpiece: Schaller Signum Bridge
Tuners: Schaller Original F Series
Strap Button: Schaller strap locks
Finish: Nitrocellulose, Hand polished
Color: Cherry burst
String Gauge: Elixir Nano Web 0.10 -0.46
Case: Harvest Leather Bag
Weight: 2.7 Kg
SPECIFICATIONS
Design: Semi Acoustic, Hand carved
Top: Solid Maple, Hand carved
Back & Sides: Solid Maple, Hand carved
Solid Center Block: At the Bridge/Tailpiece position
Body Thickness: 2'' / 50.8 mm
Body Width: 12.7'' / 32.2 cm
Binding: 7-ply, White/Black
Neck: three-piece Set Neck Maple
Neck Shape: D
Head stock: Ebony overlay
Fret board: Ebony
Pickup Rings: Handmade Ebony
Fret board Radius: 12''
Number of Frets: 22
Fret board Inlays: Yes, mother of pear